Temperature sensors come in all shapes and sizes, and have an enormous range of use cases. In this post, we take a look specifically at the ways in which IoT sensor technology is positively impacting the supply chain, and more specifically, the "cold chain."
Across the supply chain, personnel such as truck drivers and grocery workers who are responsible for temperature-sensitive goods have traditionally read temperature gauges and recorded the results on paper fastened to a clipboard. Sometimes these numbers are then entered into a spreadsheet or online database.
While this system is better than nothing, it has serious verification and reliability flaws that have implications for human health. Who can say whether the recorded temperature values actually reflect the real history of the shipment’s temperature? If the temperature fluctuates wildly over the course of being transported, and only the beginning and end points are noted, there can be spoilage that may not be detected. This is one of the reasons lettuce winds up in the news.
Until now there hasn't been a good way to prove the accuracy of those pencil-scribbled figures. Times are changing, though. With IoT, there are is a bevy of new temperature sensor devices reshaping the supply chain industry, specifically in cold chain goods, which are the most vulnerable to fluctuations in temperature.
Cold Chain: The Temperature Sensitive Supply Chain
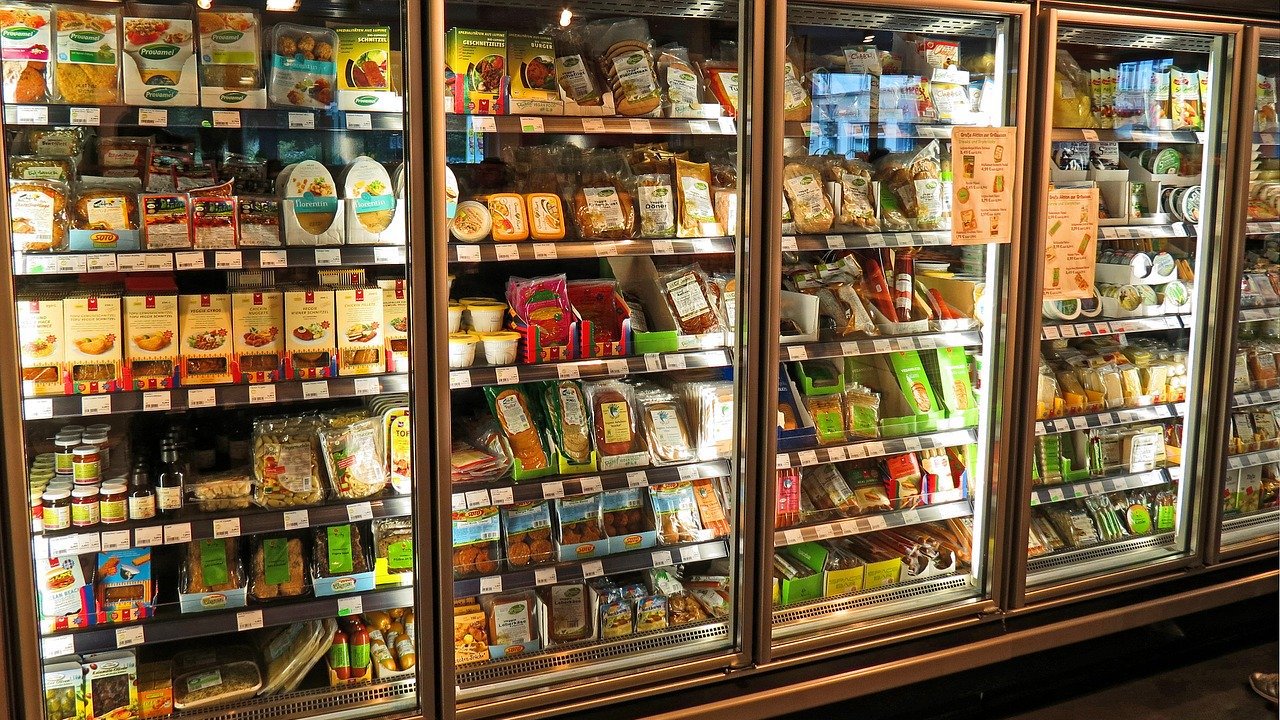
The cold chain represents the side of supply chain where careful temperature management is crucial, and encompasses the full gamut of points along the way from farming or manufacturing through shipping and final delivery to a consumer. It includes everyday products like produce, frozen food and dairy, but also pharmaceuticals which must be kept below a certain temperature, or they lose their potency and become ineffective.
In both cases, temperature monitoring and logging are critical for health and safety, and key regulations require temperature logging to prevent degradation or spoilage of product. These regulations are intended to guarantee that a product that looks safe is actually safe. Further, should a shipment arrive in poor condition, carefully kept temperature logs can reveal at what point the spoilage occurred.
For these reasons, temperature logs in trucking, retail, food service and pharmaceuticals are incredibly important, and as such they are regularly audited. But the entire system relies on the frequency, timeliness and accuracy of hand-recorded monitoring.
Critical Challenges in Cold Chain Monitoring
The problem with manually temperature logging is that the process is prone to errors. Drivers, grocery personnel and food service workers are often busy, which can result in an inaccurate or missed record. At best, a hurried misreading of the gauge, at worst, totally imaginary readings quickly jotted down to fill in for missed readings. This practice, also known as “pencil whipping,” can lead to spoiled product in the event that the logs go unchecked.
This is a difficult problem to correct for. Temperature readings can be taken as soon as a product arrives, as Target often does, but this is no guarantee that the product was kept at that temperature for the entire journey.
One way to solve for this is the Food Safety Modernization Act (FSMA), which stipulates how often temperature readings should be taken, but again, compliance depends on the driver. Certain products may become spoiled if they reach a certain temperature for even an hour or two, and if the driver fails to check the temperature at the right time, they may miss this slip. Later, if a food-borne illness outbreak occurs, it can be difficult to determine culpability or prevent the same issues from recurring.
Typically there are four key actors who are responsible for a product as it moves through the supply chain to its destination, such as a grocery, pharmacy, restaurant or convenience store. They include the loader, carrier, shipper, and receiver. This means goods – and the responsibility for monitoring them – change hands multiple times. And each of these parties may be using a different recordkeeping system.
As these flaws in cold chain temperature management come to light with new health outbreaks, organizations across the cold chain, from shipping services to retail, grocery and food service organizations, are becoming much more concerned that they could sell or serve tainted foods to their patrons. As we know, the resulting public trust crises from these outbreaks have an enormous impact on public relations, profit and loss, and business viability.
Up to now there hasn’t been a solution. However, with IoT temperature sensors and automation, it is finally possible to ensure consistency, maintain quality and ensure goods are properly monitored during packing, shipping, delivery, storage and service.
How IoT Sensors and Automation Are Revolutionizing the Cold Chain
An Internet-enabled temperature monitor can monitor goods 24/7/365. In sharp contrast with manual logging, automated monitoring enables ongoing monitoring and fast alerts, and can support a predictive maintenance program that ensures equipment is serviced before an entire truckload or restaurant refrigeration unit has spoiled.
With an IoT sensor, the temperature of a shipment is monitored and logged automatically. Those temperature readings can be viewed in near real time (typically 15 minute intervals), on any Internet-connected device from anywhere in the world.
There’s a rule of thumb that for a piece of technology to be replaced, the newer alternative has to be ten times better than the existing solution. In this case, IoT cold chain monitoring isn’t ten times better than a driver with a pencil, it’s exponentially better. Let’s look at five of the key advantages.
1. Temperature Logging is Easier
First and foremost, it makes the job of all cold chain personnel easier, as they don’t have to worry about checking temperature gauges and hand-recording temperature values. Monitoring can be done at company headquarters and the driver can be alerted only in the event that something is wrong, such as a refrigeration unit starting to fail.
2. Temperature Sensors Are More Accurate
An IoT-enabled cold chain is safer. With near 100% accuracy, it’s possible to identify shipments which have exceeded their maximum safe temperature. Disposing of a truckload’s worth of produce is a very unfortunate loss. However, it’s several orders of magnitude cheaper and less impactful than a mass recall and the cost in human health and safety and lost business.
3. IoT Temperature Monitoring Is Inexpensive
IoT temperature monitoring isn’t expensive to implement, and in fact it can pay for itself as personnel can use their time more efficiently than manually checking and recording temperatures. And in fact sensor technology itself is inexpensive. With devices like the SmartSense by Digi temperature and humidity sensor, the battery has been designed to last five years. After the upfront purchase and outside of minor on-going monitoring costs, there are virtually no maintenance costs, making it easy to budget for.
4. Temperature Sensors Are Easy to Implement
Plenty of logistics companies worry about the time it will take to upgrade their fleet, and groceries, restaurants and pharmacies have concerns about the business impact of retrofitting their monitoring systems. In the past, sensors may have required a full day or more to install. With a fleet of 50 trucks, or a chain of 50 retail stores, that would have meant 50 lost days of productivity, a major deterrent for any logistics or service organization.
However, with solutions like SmartSense logistics, food service, retail and pharmaceutical monitoring, the installation can take as little as five minutes. There’s no time-consuming drilling or threading of wires. Just find a convenient place for the sensor, attach it, and call it a day. With the sensor’s battery designed to last five years, it is a set it and forget it device that automatically sends reports, and can be checked anytime from a smartphone or tablet.
5. Real-Time Location Tracking
Finally, for those interested in the ultimate cold chain monitoring package, there is also location tracking. A SmartSense Gateway, for instance, tracks location and temperature and sends that data back to an easy-to-use dashboard. Gone are the days of a shipment being marked as “in transit.” With wireless tracking, it’s possible to know precisely where the products are and accurately predict when they will arrive.
The Future of Cold Chain Logistics
The world we’re moving towards is one in which all cold chain logistics companies, restaurants and retail stores will typically use IoT sensors to track and monitor their goods. Personnel will leave the clipboard at home, and obtain highly accurate readings taken at regular intervals that can guarantee a product was kept at the right temperature for the duration of the journey. If something goes wrong, it’s easy to figure out what happened, and whether or not the shipment is spoiled.
As more organizations and retailers discover the benefits of an IoT-enabled cold chain, there will be an industry-wide push towards adoption of the technology for improvements in accuracy and human health and safety.
Whether you want to build or buy, Digi can support your quest for temperature monitoring, for supply chain and retail management, with embedded, cellular and packaged solutions. Contact us to learn how our products, services and developer support teams can assist with your business goals.